Combing process removes predetermined level of short fibres from the group of cotton fibres. It is well known that the cotton fibres have distribution of fibre lengths starting from long to very short fibres. Figure 1 shows a typical fibre length distribution diagram for cotton fibres. |
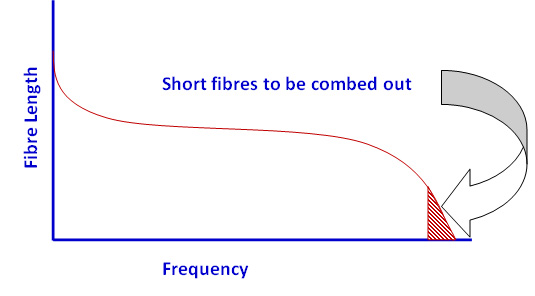 |
Figure 1. Fibre length distribution diagram |
|
The short fibres, shorter than 12 mm do not contribute to the strength of the yarn, but in turn they only increase the hairiness of the yarn and adversely affect the appearance and other good properties of the yarns and the fabrics made out of them. In the staple fibre yarn manufacturing process, only the trash particles, foreign matters and very short fibres are removed in the blow room and carding operations. In these processes, it is not possible to remove fibres which are shorter than a predetermined length, which can increase the average fibre length. In the combing operation, fibres shorter than length of fibres or certain fixed percentage of short fibres are removed. Since the shorter cotton fibres are generally coarser, removing the shorter fibres leaves behind fibres which are relatively finer. Hence, fabric made from combed cotton fibres has a very soft touch. Combing involves additional processing step and also certain amount of fibres are removed as waste. Hence, combed cotton is more expensive than conventional carded cotton. |
The texture of combed cotton is softer since it
is free from
short fibres to stick out of the yarn surface and prickle, and all dirt and impurities have been removed from the yarn. Combed cotton is also stronger since shorter and weaker fibers have been removed through combing operation. The straightened fibers lie together in a more compact manner after combing, making combed cotton yarn less likely to fray and unravel. These aspects make the garments made with combed cotton yarns an excellent choice for garments intended to be worn by babies and the elderly, since it is gentle against the skin. The soft and strong combed cotton yarns are ideal for making bed linens and clothing which will be worn against the skin. If the yarn used in a cotton fabric product is combed cotton, it can usually be clearly identified by its luster. |
On the other hand one has to keep in mind about the following shortcomings of having an additional combing section in the yarn manufacturing system. |
Shortcomings of the Combing Process :
|
 |
The combing section is an insertion of mostly three machines into the normal spinning process between card and draw frame. This needs more space with conditioned atmosphere which is becoming more and more expensive. |
 |
It serves as additional system to improve yarn quality if the carded yarn does not meet requirements. Certainly this process with three additional machines increases the cost of the yarn as it takes more energy and labour to run these machines. |
 |
The design of the comber itself is not very satisfactory since it works on intermittent processing basis which further increases the cost. |
 |
The entire mass of the nipper assembly has to be accelerated to the maximum speed and slowed down to zero about 7.5 times a second. Although it is a challenging task, the resulting intermittent processing also entails a loss in productivity. |
|
Operations in combing process : |
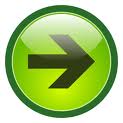 |
Elimination of a precisely predetermined quantity of short fibers. |
Elimination of short fibers improves the staple length of the combed cotton. This also results in improving the finess of raw material. The short fibres removed in the combing process is called as “noils”. It is usually referred as a percentage of the total amount of material feed to the comber. |
Noil percentage = (Weight of noil produced / Total weight of cotton fed) x 100 |
The amount of noils removed depends upon the industry and the needs ranging from 8 to 25%.Elimination of short fibers produces an improvement mainly in staple length , but it also affects the fineness of the raw material (Fig.2). Since noil is on average finer than the original raw material, the
Micronaire value
of combed sliver is slightly higher than that of the feedstock. |
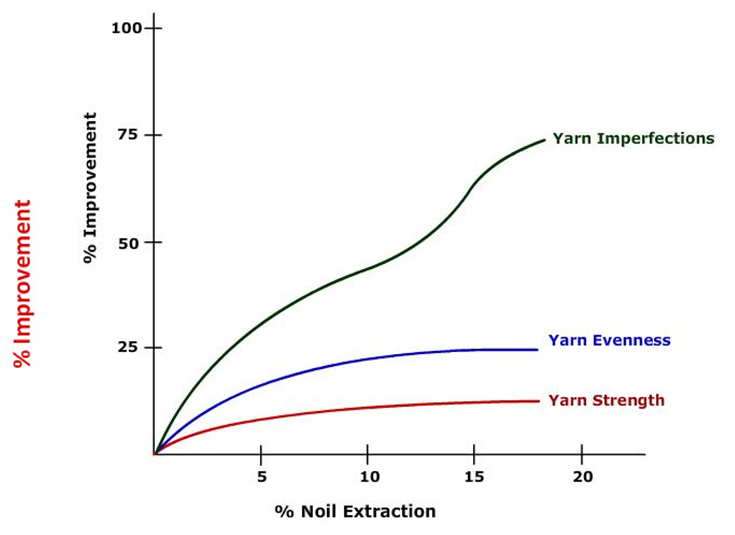 |
Figure 2 |
|
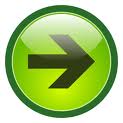 |
Elimination of the remaining impurities. |
Although most of the larger and finer trash particles and foreign already removed in the blow room and carding operations, still some fine dust particles are found to present in the carded slivers. The combing operation involves fibre treatment almost to individual fibre state. There is fibre-to-fibre rubbing and action of combing needles on the surface of fibres. These actions enable the release of fine dust particles still adhering on to the fibre surface. |
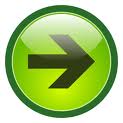 |
Elimination of neps in the fiber material. |
Most of the neps which are already present in the bale cotton and those which are introduced in the blow room operations are supposed to be removed in the carding operation. Due to improper settings and conditions in the carding operation, some of the neps still remain in the carded sliver. In the combing process, these neps get either removed or straightened due to the action of the combing needles or inter fibre rubbing and sliding. |
|
Formation of sliver having maximum possible fibre parallization. |
It should also be noted that combing increases the parallelization of the fibers, but this is a side-effect which is not always an advantage. The high degree of parallelization might reduce inter-fiber adhesion in the sliver to such an extent that the fibers slide apart, e.g. while being pulled out of the can – i.e., sliver breaks or false drafts might be caused. |
Evenness 
As the fibres are more parallel, further drafting in post comber drawing, fly frame and ring frame will introduce less unevenness. |
|
Strength 
More parallel fibres contribute better to the strength of yarn as there will be less fibre entanglements and disorientation of fibres in the yarn. |
|
Cleanness 
The high level of parallization is brought by inter-fibre rubbing and sliding which releases the finer dust particles still adhering on the fibre surface. |
|
Smoothness 
The fibres which are arranged in a highly parallel configuration give smooth surface as opposed to fibres arranged in a less parallel or random |
|
Visual appearance 
In the combing process, the short fibres are removed and the remaining longer fibres are brought to more parallel arrangement which provides more uniform appearance for the fabric as the hairs are reduced to significant levels. |
|
|
Types of Combers : |
Rectilinear comber : |
Works with stationary or oscillating nippers and is mainly used in the short staple spinning. |
Circular combers: |
Used in the English worsted process. |
Rotary comber: |
Used in the production of Schappe spun yarns |
Hackling machines: |
Used in the processing of bast fibers. |
|
The short staple spinning industry uses only the rectilinear comber with swinging nippers and stationary detaching rollers which rotate back and forth to carry out the piecing and detaching operations. It was originally developed in 1902 by the Englishman Nasmith and in 1948 by Whitin company. These machines are usually single sided comprising eight heads. |
As the course is on short staple processing, the process of cotton combing with rectilinear comber is dealt with in the following lectures. |
Goals of Combing in Different Textile Industries : |
Combing improves the quality of the yarn at the cost of removing some amount of expensive raw material with additional cost involving machinery, energy and labour. Hence the decision to use comber and remove certain amount of noil for a particular application is more of techno commercial one. Correspondingly, basic distinctions are drawn between three major groups of spinning mills using combing: |
Fine count spinning mills : |
These organizations use best quality, expensive cotton of high strength, containing a low proportion of short fibers and trash. The final product is usually a fine to very fine yarn of best quality. This puts highest demands on the know-how and skills of operating personnel. It also needs modern machines with best designs and technology with proper maintenance of the machines. In these cases, yarn production rate is less of a concern, with high generation of noil to ensure the best quality for yarns. |
Medium count spinning mills : |
In this case, cotton of medium properties with varying quality parameters are spun into medium and fine yarns of acceptable quality at reasonable economic production costs. This is becoming a more widely used process in practice. Noil extracted is in the medium range and the production rate is quite high. This is a highly competitive process in the sense that it has to yield high standard of quality at high production rate with low cost. This can be attained only with very stringent work practices with well trained personnel. |
Coarse to medium count spinning mills : |
In this case, combing is an optional process to upgrade the yarn cleanliness, smoothness and strength. This may use the same raw material used for producing carded of the same count. Because of additional combing process, in comparison with a carded yarn, the combed yarn exhibits better yarn properties. Again in this case the production rate and cost of production is not compromised with improved quality with removal of noils in range of 8 to 18%. In case of fine counts combing is an essential process in order to get the minimum number of fibres after removing certain amount of short fibres, where as in this case it is only optional. |
Components involved in Combing |
Click on Image to run the animation |
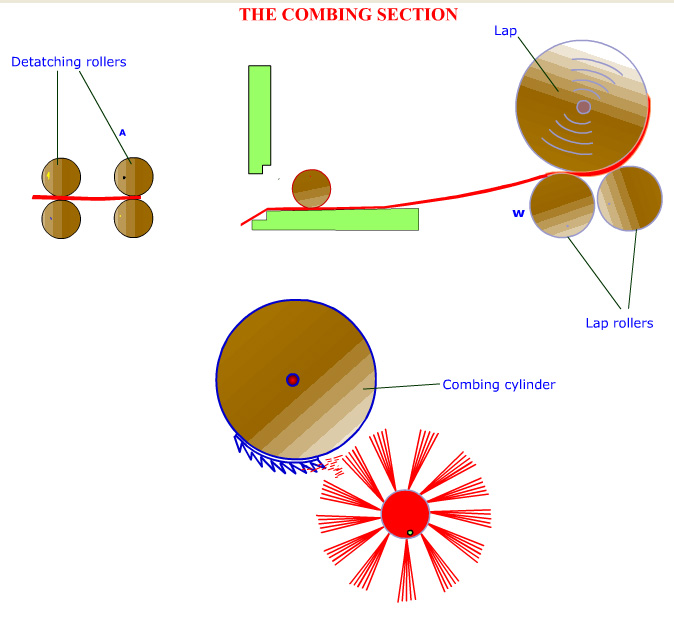 |
|
Sequence of operations in a Comber : |
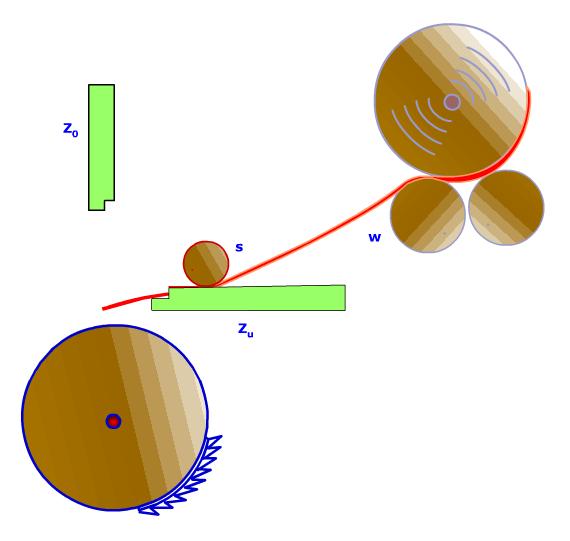 |
Feed rollers move the lap by 4-6.5 mm . |
|
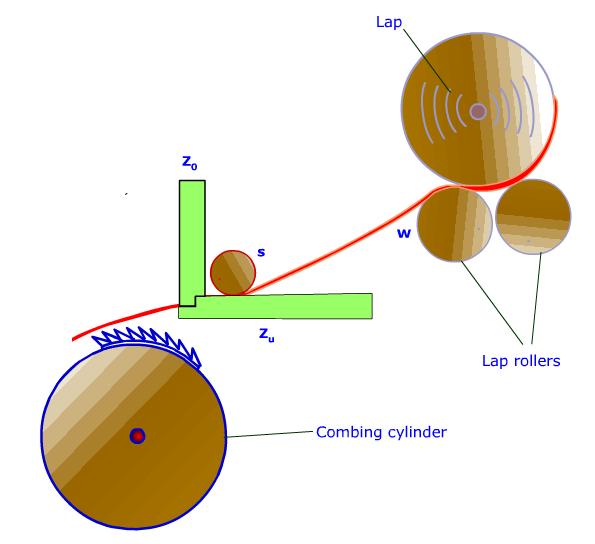 |
Upper nipper plate Z 0 is lowered and the fibers are nipped |
|
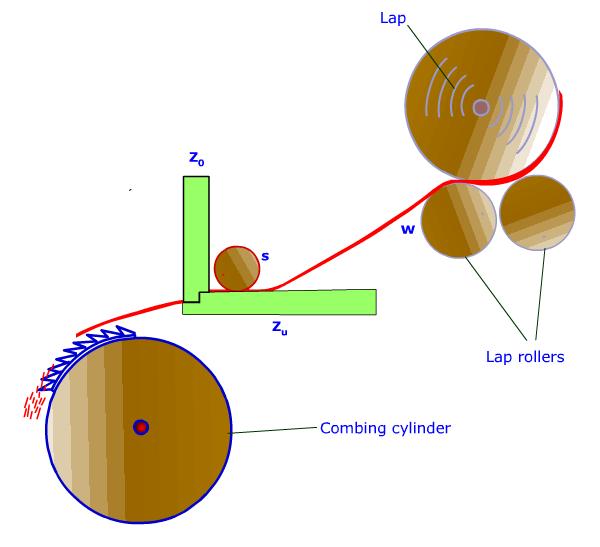 |
Combing segment k combs the fiber fringe and Carries away those fibers not held by nippers
|
|
 |
Nippers open again and move towards the detaching rollers.
|
|
 |
Detaching rollers rotate backwards and bring back a part of the material
|
|
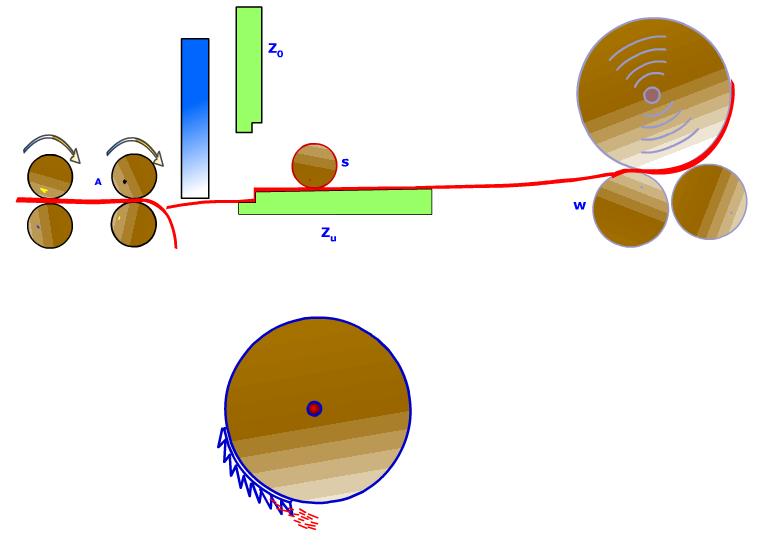 |
The new fiber (B) fringe is placed over the returned material (V)
|
|
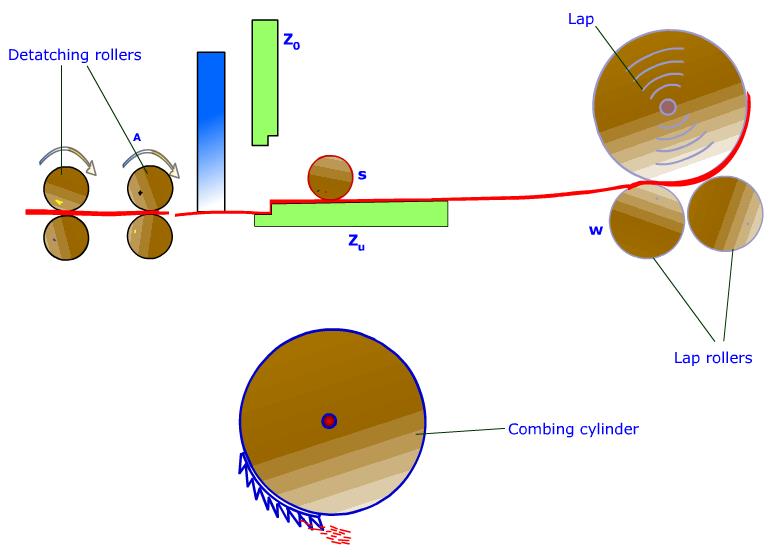 |
Detaching rollers reverse the direction and draw the clamped fibers out of sheet W.
|
|
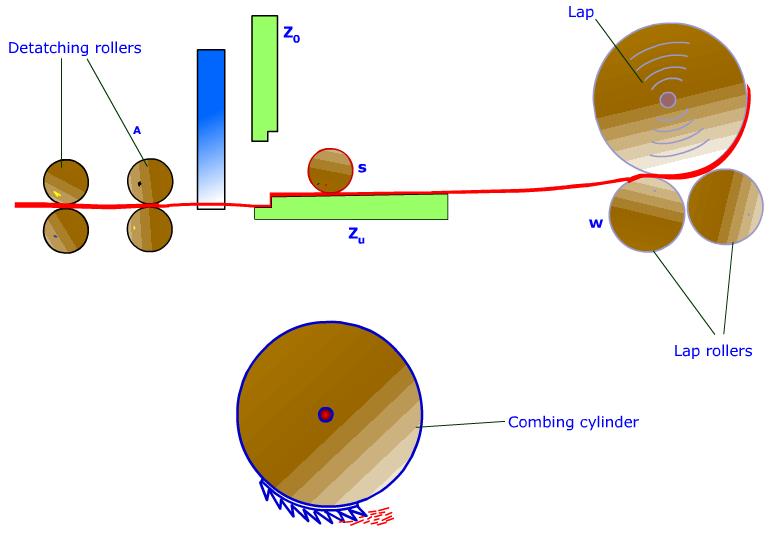 |
The top comb thrusts its single row of needles into the fibe fringe.
|
|
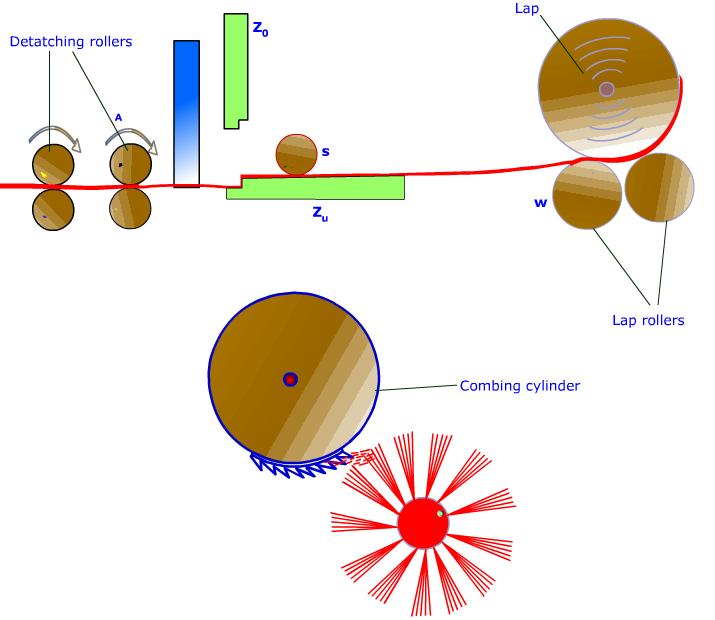 |
Nipper assembly moves back. Top comb is withdrawn and new cycle begins. Combing segment is cleaned by the brush roller.
|
|
 |
Feed rollers (S) move lap sheet (W) forward by a small amount (4.3 - 6.7 mm), while nippers (Zo/Zu) are kept open (feed). |
 |
Upper nipper plate Zo is lowered onto cushion plate (Zu) so that the fibers are clamped between them (nipping). |
 |
Combing segment (K), mounted on rotating cylinder (Z), sweeps saw-teeth through fiber fringe (B) and carries away anything not held by the nippers (rotary combing). |
 |
The nippers open again and move toward detaching rollers (A) (nippers forward). |
 |
Meanwhile detaching rollers (A) have returned part of the previously drawn-off stock (web V) by means of a (partial) reverse rotation, so that the web protrudes from the back of the detaching device (web return). |
 |
In the course of the forward movement of the nippers, the projecting fiber fringe (B) is placed on the returned web (V) (piecing). |
 |
The detaching rollers begin to rotate in the forward direction again and draw the clamped fibers out of web (W) held fast by feed rollers (S) (inside the nippers) (detaching). |
 |
Before the start of the detaching operation, top comb (F) has thrust its single row of teeth into the fiber fringe. As the fibers are pulled through the teeth of the top comb during detaching, the trailing part of the fringe is combed, thus making up for the inability of the circular combs to reach this part of the fringe (passive combing by the top comb). |
 |
As the nipper assembly is retracted, the nippers will open for the next feeding step. During that time top comb will withdraw and the system is ready for new combing cycle |

|
Contrary to the movements of the other parts, the combing cylinder rotates continuously. During this rotation and at a certain instant the combing segment is brought into the vicinity of a rapidly revolving brush mounted below the combing cylinder. During this processThis the brush removes the imperfections, dust etc., from the combing segment, and ejects them into an extractor that carries the noil away to a collecting filter system. |
 |
All these demanding processing steps are carried out mechanically on 8 combing heads which are simultaneous process at speed up to 500 times per minute. |
|
|
Sources : |
- W. Klein, “Technology of Short Staple Spinning”, The Textile Institute, Manual of Textile Technology, All volumes.
- Carl A. Lawrence , “ Fundamentals of Spun Yarn Technology”, CRC Publications, 2003.
- P.R. Lord, Hand Book of Yarn Production : Science, Technology and Economics, Tailor and Francis, 2003.
- Eric Oxtoby, “Spun Yarn Technology”, Butterworths, 1987.
- NCUTE publications on Yarn Manufacturing, Indian Institute of Technology, Delhi.
|
|